Case Study – Prometheus Colorimeter for Demanding Display Applications
Electro Optics interviewed our CEO Steven Goetstowers to learn about the latest Prometheus colorimeter series.
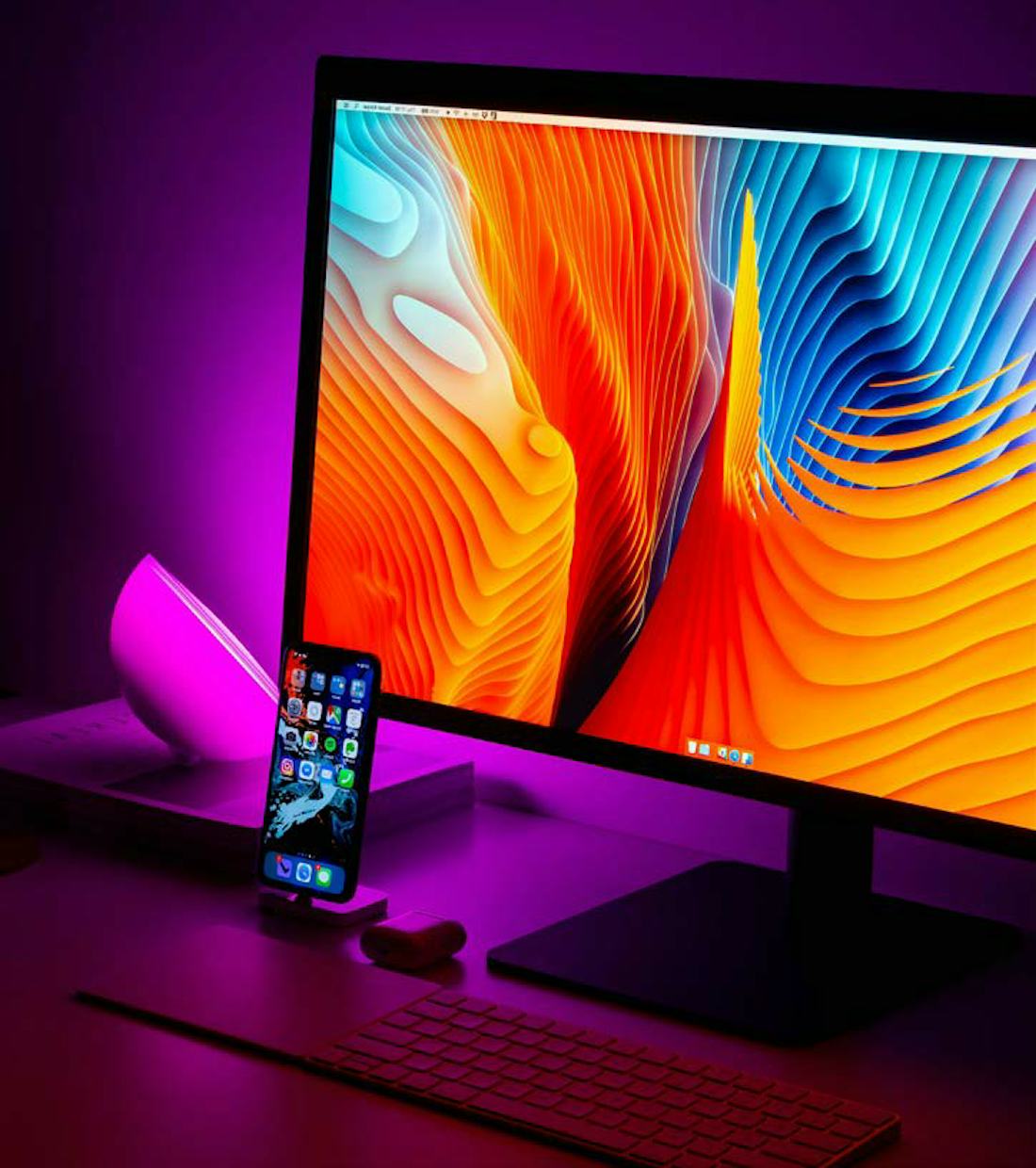
Display color measurements – getting it right without compromise
The consumer electronics industry is a multi- billion-dollar market, with the latest figures from data firm, Statista, predicting a worldwide spend of around $2.06tn by 2023 on consumer electronics devices. To offer an example, according to independent research firm, Strategy Analytics, almost half of the global population now owns a smartphone. This is without taking into account televisions, AR and VR technology, wearables, voice technology and other consumer products. In such a busy and competitive market, with new players entering at pace, it is essential for manufacturers to be able to operate at maximum efficiency, both to meet demand and to ensure quality levels are of the same high standard in every product produced. This is certainly the case when it comes to the displays for these products, as Steven Goetstouwers, CEO at Admesy, has witnessed over the last 15 years through the company’s work with some of the leading consumer electronics manufacturers. ‘It is important that all consumer devices sold in a shop look the same, according to brand, to the end customer,’ he explained. ‘There should be nothing obvious, such as, for example, a display having a yellow tone when it should be white.’
Repeatability as standard
To ensure this is the case, manufacturers require incredibly accurate and yet very fast colour measuring equipment. ‘It has to be accurate, because the human eye is extremely adept at spotting colour differences,’ said Goetstouwers. ‘It has to be fast, because with consumer electronics applications, they’re not building one device, they’re building tens of millions.’ One particular application led to Admesy collaborating with a customer to provide a particular colorimeter. ‘Manufacturers are now putting items underneath the display,’ explained Goetstouwers. ‘For instance, they are building fingerprint scanners, cameras or facial recognition under the display, to produce a phone, tablet or a laptop without a border or a cut-out for a camera. But this can weaken the part of the display with the item underneath it.’ This means there is a potential spot where the performance of a display might differ, and this particular customer had the requirement to measure this point to ensure this particular part of the display had the same performance as the rest of the display. ‘The challenge,’ continued Goetstouwers, ‘is that it had to be small, and to go small, you have to start with an extremely fast colour measurement.’ This is due to the risk that a smaller size could reduce the measurement speed. ‘You need a very fast device to start with,’ he explained, ‘because you know you could lose a lot of speed by focusing-in, and you need a very complex lens system to still get a relatively fast sampling speed. We also ran into a very interesting, practical aspect: at this size, how do you still know that you’re looking at the right spot?’
“Display measurements have to be fast, because with consumer electronics applications, they’re not building one device, they’re building tens of millions”
To compare, traditionally the measured spots in a display would be 10 or 20mm and they would be in the centre, which would allow for a certain margin of error. ‘Now,’ said Goetstouwers, ‘because it’s such a small spot, if you miss a line, even only briefly, the measurement spot and the spot size don’t align well and the illuminance values could be incorrect.’
The solution
This was solved by putting in an alignment light in the centre of the measurement spot, so instead of only measuring, the colorimeter can also send a red LED dot, which can be used to check with the camera to ensure it is where it is supposed to be. ‘That information can be used to ensure the holes are aligned properly,’ revealed Goetstouwers. The team at Admesy also noticed that other customers were experiencing similar requirements. ‘We basically went from providing just the sensor and measurement tool, to more of a full system because now there is an alignment tool included, and if the data is read correctly, the positioning of the display or the measurement can be adjusted based on that information.’ The result of the project is the Prometheus series of colorimeters, which is now available to all customers, thanks to a lot of hard work and cooperation between Admesy’s optical and mechanical engineers. ‘This whole lens design is one of the more complex ones we have done,’ said Goetstouwers. ‘And the engineers were able to build it in such a way that it is scalable using a normal production process.’ The Prometheus series includes flicker and response time measurement options to the colour measurements and offers a larger dynamic range and increased sampling speed than its predecessor, the Hyperion colorimeter. It is also designed to be robust for 24/7 use, and easy to integrate in production environments. A number of different lenses are available. For general display measurements there are collimating lenses with 10, 20 or 27mm spot size. For smaller areas of interest, or special applications like those detailed in this case study, a focusing lens version with 2.1 or 5mm spot size is also an option.